Military ships must undergo technical inspections at specified intervals. At the same time, necessary modernization work is carried out. In the Wilhelmshaven naval arsenal, the frigate “Hamburg” is currently undergoing so-called depot repairs.
While the ship is in port, all wear and tear parts of the ship are put through their paces and replaced if necessary. In addition, product changes or additions that have become necessary are implemented as well as extensive safety checks. This includes, for example, checking the tanks and ventilation systems. Even conversions that have to be carried out due to changed general standards are among the challenges in depot repairs.
At the beginning of all necessary work, however, there is always the concrete planning of the processes.
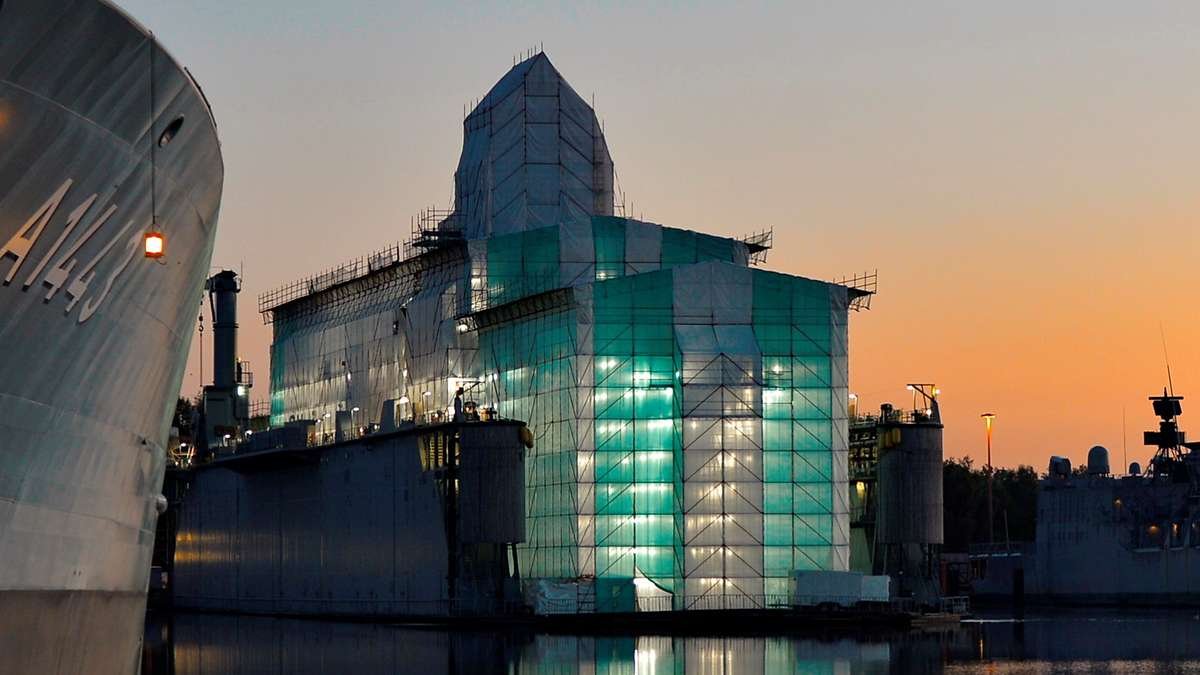
After all, once a ship has arrived at the naval arsenal’s construction site, everything has to be just right. All measures must be able to be carried out smoothly and without major delays, hand in hand. A big challenge, because on some days several hundred people are busy on or at the ship at the same time.
The repair officer and his team are therefore working towards this point for a whole year and plan all the processes down to the last detail. What happens when and where on the ship will not be left to chance.
In addition, well in advance of a depot repair, all the necessary trades are advertised externally in accordance with the legal requirements. Because the actual implementation of the work is largely carried out by specialist companies whose services have to be logistically coordinated.
Inside the frigate, you can quickly see that it has turned into a major construction site. Metal lattice boxes with pipes and covers that have been dismantled and previously carefully marked can be found in almost every free corner.
Makeshift, transparent hoses are laid everywhere. This is used for the external air conditioning of the ship and the extraction of dust and gases that arise during hot work.
The controlled climate on board also ensures that no condensation can form. This is important for the conservation work on the ship’s hull, but also for all the electronics on board, which could otherwise be damaged.
Countless temporary cables for the lighting and for operating the work equipment have also been laid.
Before the company employees can get on the ship and get started, however, the experts from the naval arsenal are needed first.
During the so-called “naval arsenal layover period 1”, these experts remove all military weapon, radar, sonar and electronic systems from the ship: Because these are always maintained and repaired in “arsenal operation” as a core task of the naval arsenal.
“What’s left of the frigate can be described something like this: imagine a cruise ship a good 300 meters long and almost 45 meters wide with all the technology built into it, which has now shrunk to 143 meters long and a good 17 meters wide becomes. The result is a small, extremely densely packed ship,” explains one of the team’s engineers.
Even if you don’t carry them out yourself – all ship repair measures are intensively supported by the experts from the naval arsenal.
For example, they ensure that all work is completed within the specified time frame. And they are there when you need to react quickly to unforeseeable challenges.
For example, the engines on the frigate “Hamburg” are being swapped out. The previously installed ones are overhauled after around 30,000 operating hours – many times the total mileage of a normal car engine. Specialists in engine and ship mechanical engineering are required for this task.
The situation is completely different when it comes to renovating the accommodation cabins. For their demolition, for example, not only do walls have to be removed, but all electrical and water-carrying lines have to be professionally disconnected beforehand. In addition – almost like in a house – there are also specialists for interior design and for painting and varnishing work.
Due to the now higher hygiene standard in food processing, the equipment in the galley on the frigate “Hamburg” also has to be adapted. The cooking group and counter are replaced via a newly created opening in the ship’s outer skin. To do this, the entire interior paneling including the insulation of the ship’s hull must be removed and all power and water connections must be dismantled.
After the installation of the new equipment and the closing of temporary openings in the outer skin of the ship as well as the restoration of the interior paneling, the “construction management” of the naval arsenal is called upon again. She carries out quality assurance and creates the completion report for all repair work. The repair officer carries out the final acceptance of the commercial services shortly after the shipyard test drive lasting several days.
During the shipyard test drive, the ship is checked in detail in normal seafaring operation. This is followed by the so-called “naval arsenal rest period 2″, during which the repaired and tested weapon, radar, sonar and military electronic systems are reinstalled by the naval arsenal’s specialist staff.
After extensive tests in the port, the ship finally sets sail to prove its operational capability in multi-day function tests. Only after all tests have been successfully completed will the ship be returned to the German Navy.
“We not only accompany a ship throughout the entire repair process. This also includes the shipyard test drive as the conclusion of the services provided by the commercial sector – and of course the handover of the overhauled ship to the German Navy,” explains the repair officer.
However, the Naval Arsenal team does not have much time after that. The next Navy ship has already been registered for depot repairs.